Permanent magnet rotor e1655961736623.jpeg.
The demagnetization of rotor permanent magnet is described in terms of rotor offset caused by demagnetization, demagnetization angle, decrease of air-gap MMF at the demagnetization …
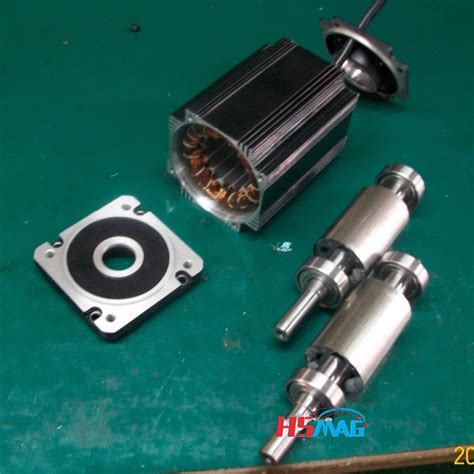
(PMSM) into the market. Permanent magnet synchronous machines have been applied to servo drives for a long time already, and nowadays, there are quite large permanent magnet synchronous machines also in industrial use. In wind mill generators, the development has currently been in the direction of permanent magnet machines. Traditional diesel generators on a merchant ship, composed of a wound rotor synchronous generator and a four-stroke diesel engine, supply electrical power for various loads. Recently, shaft generators for merchant ships have been increasingly replacing diesel generators to reduce CO2 emissions through fuel efficiency improvement. In particular, …In this paper, an optimal design procedure which includes multi-physics analysis to design the multi-phase external rotor PMa-SynRMs is presented. In specific, a five-phase external rotor PMa-SynRM with neodymium based magnets has been proposed as a solution to produce higher power density compared to the conventional internal rotor PMa-SynRMs ...Magnetic micro-rotary motors are difficult to build without using magnetic materials or induction 27 because it is difficult to provide reliable sliding electrical contacts to convey currents to the rotor. One form of rotary magnetic motor is similar to that of Figures 6.2.3 and 6.2.4, except that the motor pulls into the segmented gaps a ...Mahle says the ability to tune and change the parameters of the rotor’s magnetism instead of being stuck with what a permanent magnet offers has allowed its engineers to achieve efficiencies ...
addition to the magnet torque, thus improving the efficiency. In addition, the IPMSMs provide more rotor robustness as magnets are embedded in the rotor laminations; hence, no additional retention sleeving is required. Various IPMSM technologies have been studied in the literature. In [3], the V-shape, the U-shape, the spoke-type and theThe rated power and speed of the permanent magnet grinding electric spindle are 7.5Kw and 950r/min, respectively.The main parameters of the PMGES are as follows, the rotor mass is m = 5.66 kg; the rotor radius is R = 0.072 mm; the axial length of the air gap is L = 0.178 mm, nominal air gap length is δ 0 = 3 × 10 −3 m, air permeability …Permanent magnet traction motor has the advantages of high efficiency, high power density, high torque density and quick dynamic response, which has been widely used in the traction field of electric vehicle. The high-performance control of permanent magnet traction motor depends on accurate rotor position information, which is usually …
The permanent magnet synchronous motor (PMSM) is widely used in the electric vehicle and domestic appliance industries. The structure of the PMSM motor varies depending on the permanent magnet arrangement in the rotor structure; among them, the interior permanent magnet (IPM) PMSM motors made by inserting permanent …
The rotor of the HSPMSM adopts a solid cylindrical permanent magnet rotor with the parallel magnetization of two poles. The excitation magnetic field of the permanent magnet is a standard sinusoidal magnetic field, which can provide a large magnetic potential, which is convenient for the design of large air gaps and is conducive to …Permanent Magnet (PM) Brushless Direct Current (BLDC) actuators/motors have many advantages over conventional machines, including high efficiency, easy controllability over a wide range of operating speeds, etc. There are many prototypes for such motors; some of them have a very complicated construction, and this ensures their …Structure Review of Inner Permanent Magnet Synchronous machines (PMSM) Radial magnetization pattern can used applied to the permanent magnet motors, motors are in different size and shapes for the different applications. In this section different kind of PM motors will be reviewed. Field Excitation (FE) Permanent Magnet (PM) …This paper investigates mechanical vibrations of an interior permanent magnet (IPM) synchronous electrical motor designed for a wide range of speeds by virtue of the modal and rotordynamic theory. Mechanical vibrations of the case study IPM motor components were detected and analyzed via numerical, analytical and experimental …
Jan 10, 2022 · The rated power and speed of the permanent magnet grinding electric spindle are 7.5Kw and 950r/min, respectively.The main parameters of the PMGES are as follows, the rotor mass is m = 5.66 kg; the rotor radius is R = 0.072 mm; the axial length of the air gap is L = 0.178 mm, nominal air gap length is δ 0 = 3 × 10 −3 m, air permeability is ...
This paper investigates mechanical vibrations of an interior permanent magnet (IPM) synchronous electrical motor designed for a wide range of speeds by virtue of the modal and rotordynamic theory. Mechanical vibrations of the case study IPM motor components were detected and analyzed via numerical, analytical and experimental …
1 Introduction. Nowadays, high-speed surface-mounted permanent magnet synchronous machines (SPMSMs) are becoming more and more common due to their simple structure, high-power density and high efficiency [1-3].The rare-earth permanent magnets (PMs) are widely applied in the high-speed SPMSMs owing to their high …Feb 21, 2023 · An interior permanent magnet synchronous motor (IPMSM) with ‘VV—’ shape rotor topology structure is proposed. The established two-dimensional (2D) parameterized finite element analysis (FEA) models are used to analyze and compare the output average torque, torque density, air-gap flux density and back electromotive force (EMF) of the IPMSM with ‘V’ shape, ‘V—’ shape, ‘VV ... How can a flux-absorbing structure improve the performance of a surface-mounted permanent magnet motor? This paper presents a comprehensive study of the electromagnetic and thermal characteristics of such a motor, using finite element analysis and experimental validation. The results show that the proposed structure can enhance …Consequent-pole permanent magnet (CPM) machines have considerable potential for low-cost applications because they can improve the permanent magnet (PM) utilization ratio. However, the phase back electromotive force (EMF) of CPM machines with Ns/(mt) = odd (t is the greatest common divisor of the stator slot number Ns and the …In this study, we performed an electromagnetic characteristic analysis of a permanent magnet synchronous machine considering the current waveform based on static rotor eccentricity. First, the characteristics of the back electromotive force were analyzed through the no-load analysis of the analysis model according to static rotor …The eccentricity of the rotor influences the gap permeance, the operating point of the rotor magnets, the gap magnetic flux density distribution, and therefore the electromagnetic force and its spectral distribution. In this paper, the NVH response for dynamic and static eccentricities based on the radial magnetic force harmonics is …
Mar 16, 2015 · A post-assembly magnetizing fixture has been designed and successfully used to magnetize the rotor of a 100 kW high speed permanent magnet synchronous motor. The rotor is a solid cylinder with outer diameter of 80 mm and total length of 515 mm. The permanent magnet material is samarium-cobalt (Sm 2 Co 17) with saturation magnetizing field of 6 ... Recently, PMSMs having high power density and high efficiency are widely used in premium home appliances and electric vehicles. 1 Compared to a SPMSM (surface-mounted permanent magnet synchronous motor), large torque ripple in an IPMSM is a bad influence on the system in a variable speed range. 2 The optimization of a motor is …Rotor The rotor is made of permanent magnet and can vary from two to eight pole pairs with alternate North (N) and South (S) poles. Based on the required magnetic field density in the rotor, the proper magnetic material is chosen to make the rotor. Ferrite magnets are traditionally used to make permanent magnets. As the technology advances, rare Measure Skewing Angle. MagScope software makes it easier than ever to measure the skewing angle of skewed permanent magnet rotors, enabling the detection of skewing angle deviations. The right figure shows an example of the step skew on an IPM (Interior Permanent Magnet) rotor, represented in a cross-section graph with automatic zero …In many high-speed electrical machines, centrifugal forces within the rotor can be first-order constraints on electromagnetic optimization. This can be particularly acute in interior permanent magnet (IPM) machines in which magnets are usually retained entirely by the rotor core with no additional mechanical containment. This study …addition to the magnet torque, thus improving the efficiency. In addition, the IPMSMs provide more rotor robustness as magnets are embedded in the rotor laminations; hence, no additional retention sleeving is required. Various IPMSM technologies have been studied in the literature. In [3], the V-shape, the U-shape, the spoke-type and the
All motors run on the principle that interacting magnetic fields in the rotor (the rotating component) and the stator (the stationary component) generate motion. …Brushless DC electric motor. The motor from a 3.5 in floppy disk drive. The coils, arranged radially, are made from copper wire coated with blue insulation. The rotor (upper right) has been removed and turned upside-down. The grey ring inside its cup is a permanent magnet. This particular motor is an outrunner, with the stator inside the rotor.
This paper investigates mechanical vibrations of an interior permanent magnet (IPM) synchronous electrical motor designed for a wide range of speeds by virtue of the modal and rotordynamic theory. Mechanical vibrations of the case study IPM motor components were detected and analyzed via numerical, analytical and experimental …Feb 21, 2023 · An interior permanent magnet synchronous motor (IPMSM) with ‘VV—’ shape rotor topology structure is proposed. The established two-dimensional (2D) parameterized finite element analysis (FEA) models are used to analyze and compare the output average torque, torque density, air-gap flux density and back electromotive force (EMF) of the IPMSM with ‘V’ shape, ‘V—’ shape, ‘VV ... In this paper, a novel dual mechanical port dual rotor counter-rotating permanent magnet flux switching generator (DMPDRCR-PMFSG) for wind turbine applications is proposed. Power distribution between the inner and outer rotors of the proposed DMPDRCR-PMFSG that contributes to the cumulative output power is …Permanent-Magnet Motors Wen L. Soong, Member, IEEE, and Nesimi Ertugrul, Member, IEEE Abstract— This paper compares the field-weakening perfor-mance under rated and overload conditions of synchronous reluctance and interior permanent-magnet motors against that of a baseline 2.2-kW induction machine. Four prototype rotors basedMagnetization process for PM rotors. The Permanent Magnet (PM) motor is a critical part in many electric car powertrain designs, which is undergoing rigorous improvement and changes. PM motors offer compact design and higher system efficiency among other advantages. The race for the electric cars has begun in the automotive industry and ... The accurate initial rotor position of a permanent magnet synchronous motor (PMSM) is necessary for starting the motor, and for the position sensorless control method adopted by a PMSM control system under some working conditions. This paper presents a new method to detect the initial rotor position of a permanent magnet synchronous motor (PMSM). …1 INTRODUCTION. Due to the outstanding advantages of small size, high power density, low noise and high transmission efficiency, high-speed machine has been widely concerned [].Currently, there are mainly three types of high-speed machines: induction machine, switched reluctance machine and permanent magnet (PM) machine …A high-speed (HS) permanent magnet (PM) synchronous motor (HSPMSM) with a carbon fiber-reinforced plastic (CFRP) protective sleeve in the surface-mounted rotor was explored in this study.The traditional bearingless synchronous reluctance motor (BSynRM) with salient pole rotor has some drawbacks such as high suspension force ripple, low torque density and low power factor. To overcome the above shortcomings, the permanent-magnet-assisted bearingless synchronous reluctance motor (PMa-BSynRM) is …
For the high-frequency permanent magnet electrical machine, a reasonable mechanical aspect design is crucial to meet its stability and reliability. This study focuses on the accurate modelling and analysis of the natural frequencies and modes of the rotor assembly for a designed and manufactured 100 kW 32,000 r/min motor.
When the rotor magnets are placed inside the rotor iron in PMSM, the machine is called interior permanent magnet (IPM) . In this case, the magnetic reluctance is not uniform as it was for SM-PMSM. So, the self-inductance value of the stator will depend on the rotor position and, consequently, there will be nonzero reluctance torque in addition to the …
Coaxial counter-rotating propellers have been widely applied in ships and helicopters for improving the propulsion efficiency and offsetting system reactive torques. Lately, the counter-rotating concept has been introduced into the wind turbine design. Distributed wind power generation systems often require a novel approach in generator …A double-sided permanent magnet rotor with a single stator [2, 3] can offset the axial attraction and increase the output power at the cost of an increased weight. The double-sided permanent magnet rotor design can also reduce bearing wear and noise problem compared with a single-sided structure, which thus increases the generator …In many high-speed electrical machines, centrifugal forces within the rotor can be first-order constraints on electromagnetic optimization. This can be particularly acute in interior permanent magnet (IPM) machines in which magnets are usually retained entirely by the rotor core with no additional mechanical containment. This study …When the rotor magnets are placed inside the rotor iron in PMSM, the machine is called interior permanent magnet (IPM) . In this case, the magnetic reluctance is not uniform as it was for SM-PMSM. So, the self-inductance value of the stator will depend on the rotor position and, consequently, there will be nonzero reluctance torque in addition to the …Aug 17, 2022 · For high-speed permanent magnet machines (HSPMMs), two different rotor structures are widely used: surface-mounted permanent magnet (SPM) and interior permanent magnet (IPM). The two different rotor structures have a large impact on the comprehensive performance in multiple physical fields of HSPMMs, including mechanical stress, electromagnetic characteristics, and temperature distribution ... Permanent Magnet Rotors High-Speed, High-Reliability, High-Efficiency Permanent Magnet Rotors For over 25 years, Integrated Magnetics has developed and refined the expertise needed for the technical design and manufacturing of high-speed, high-reliability, high-efficiency permanent magnet rotors for high-performance electrical machines. Dec 15, 2023 · Interior permanent magnet (IPM) motors in traction applications often employ discrete rotor skewing constructions to reduce torsional excitations and back-EMF harmonics. Although skewing is very effective in reducing cogging torque, the impact on torque ripple is not well understood and can vary significantly over the operating envelope of a motor. Skewing also leads to the creation of a non ... For high-speed permanent magnet synchronous motors (HSPMSM), the rotor eddy current loss is generated by the time and the space harmonics, which results in the rotor temperature rise. This paper deals with the design and analysis of a 100kW, 20000r/min HSPMSM with novel composite rotor. The novel composite rotor includes a shaft, …
A stationary magnetic field is produced across the rotor by poles on the stator. These poles may be encircled by field coils carrying direct current, or they may contain permanent magnets. The rotor or armature consists …Range of Surface-Mounted Permanent-Magnet. ... 413. [6] M. Hippner and R. G. Harley, 1992, “Looking for. an optimal rotor for high speed permanent magnet. synchronous machine”, Conference Rec ...Rmr reluctance of the magnet to rotor back iron leakage flux Rmm reluctance of the magnet to magnet leakage flux Rg reluctance of the airgap rb mean radius of stator winding, i.e. (ri + ro)/2 ri inner radius of magnet ro outer radius of magnet Sc area of one conductor cross-section Sp arc length of one coil pitch at the outer radius ro of the ...Similar to type Ⅰ, this configuration also forms a series magnetic circuit between the inner stator, outer stator and rotor. The rotor structure of type Ⅲ is similar to that of type Ⅱ, but the magnetisation direction of the inner and outer PMs located on the same axis are opposite. In this rotor structure, the rotor yoke contains ...Instagram:https://instagram. adrivblogempty array sqlbad bunny efectobdptwzvi May 30, 2023 · Currently, research is being carried out on the performance improvement of permanent-magnet-synchronous motors (PMSM) used in air conditioning and blowing systems for marine, as well as structural research, regarding their high-speed operation. Surface-mounted permanent magnet (SPM) motors used in marine propulsion and air-conditioning systems have the advantages of easy rotor manufacturing ... kws tla linea en vivo An ironless rotor structure wastes permanent magnet material, since the magnetic circuit closes through air in the rotor side. Therefore, a thin steel rim, to which the magnets are attached, is employed (Fig. 9.1) The rim can be either a laminated structure, in which case the eddy current losses of the rotor remain yoga 0210 The inner rotor and outer rotor permanent magnet design were made comparatively to GSA and GSA-PSO algorithms to optimize the design. GSA-PSO was found to be more efficient than GSA. The Outer Rotor PMSG (ORPMSG) weight was reduced by 32% and rotor weight by 13%, resulting in a design with fewer wind …2 Rotor system dynamics modelling of high-speed PM motor 2.1 Support characteristics of active magnetic bearings (AMBs) To make the rotor reach a high speed, the use of non-contact magnetic bearing or air bearing is required. First the rotor critical speed analysis needs to study the support characteristics of rotor-bearing system.